CRAFTSMANSHIP: HOW WE MAKE OUR BESPOKE FINE JEWELLERY
Quality and craftsmanship are at the heart of everything we do. Each piece of McCaul Goldsmiths’ jewellery is hand-crafted and finished to the highest standard. We pride ourselves on creating unique modern fine jewellery that will last for generations. Our jewellery is made using a combination of traditional hand-making techniques and cutting edge technology. As award-winning goldsmiths, designers and diamond-setters with years’ of experience we have exacting standards and are confident in our ability to deliver unique modern design and impeccable craftsmanship. Find out how we create our modern fine jewellery below.
TRADITIONAL SKILLS
Traditional goldsmithing skills are integral to our work. Centuries-old processes such as hand-forging, hammering, carving and engraving can be seen throughout our collections. Much of our design is process-led, with our collections evolving as we explore and perfect technique.
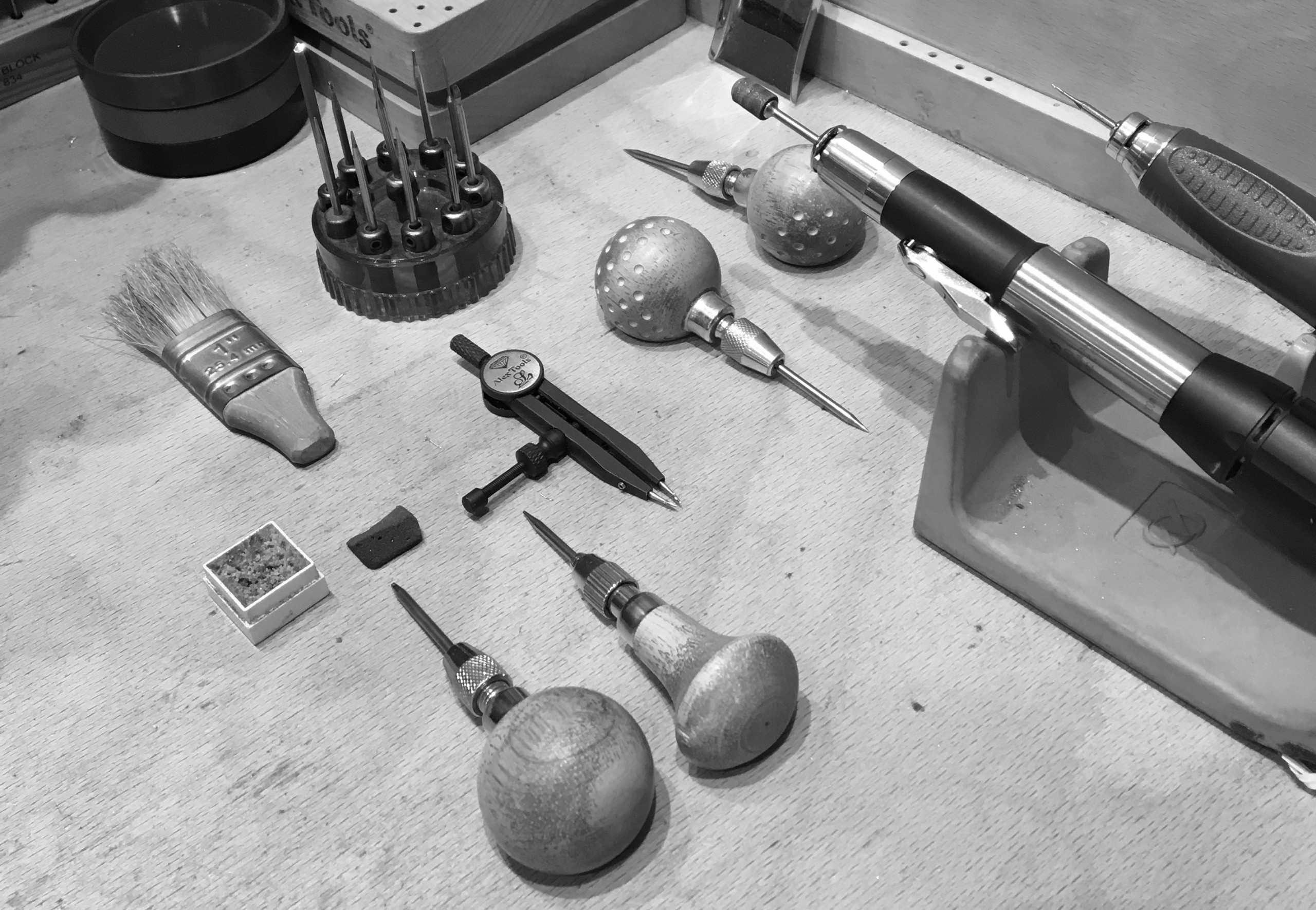
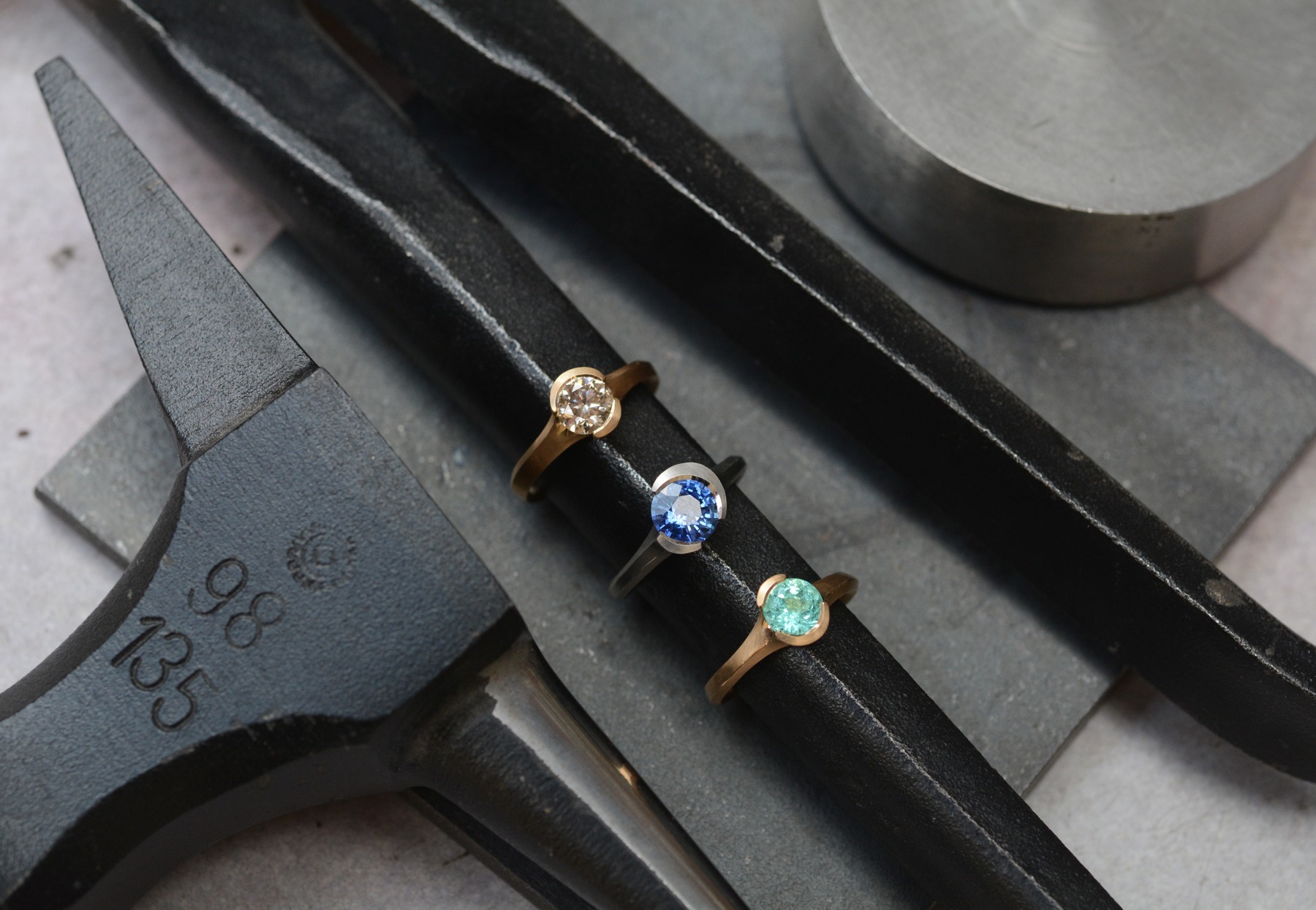
DESIGNED, MADE AND SET IN-HOUSE
Every piece of our jewellery is designed, made and set in-house. We have over 20 years’ experience in bespoke jewellery making and diamond-setting so you can be confident that your jewellery will last for generations. Our London atelier combines a shop display space with our workshop and you are welcome to come in and watch us at work.
AWARD-WINNING DESIGN
Our award-winning designs range from elegant, modern engagement and wedding rings to unique statement pendants, earrings and dramatic cocktail rings. We specialise in bespoke jewellery design and many of our pieces are unique creations commissioned by clients. Bespoke designs usually begin with sketching and may involve model making in wax or metal.
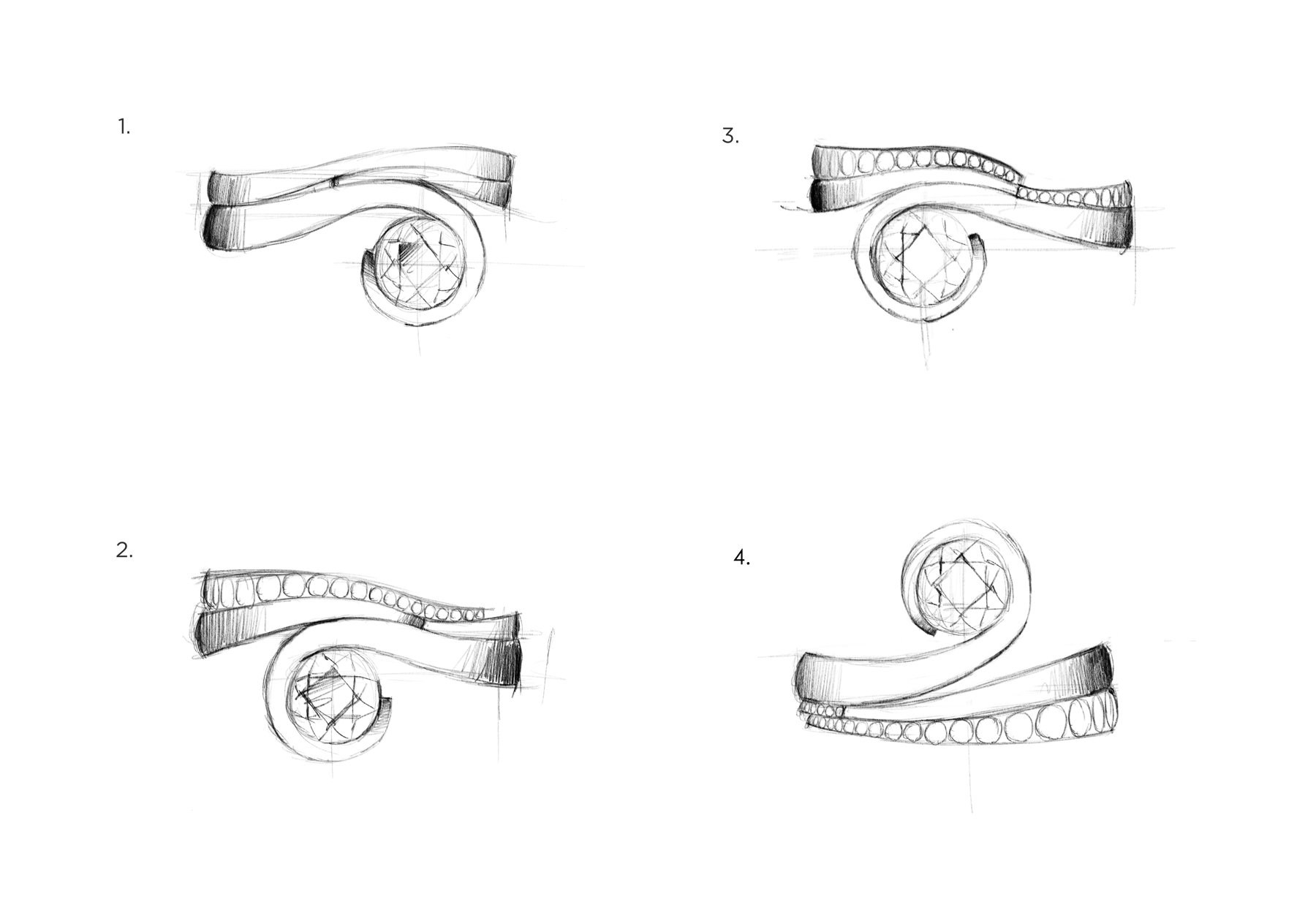
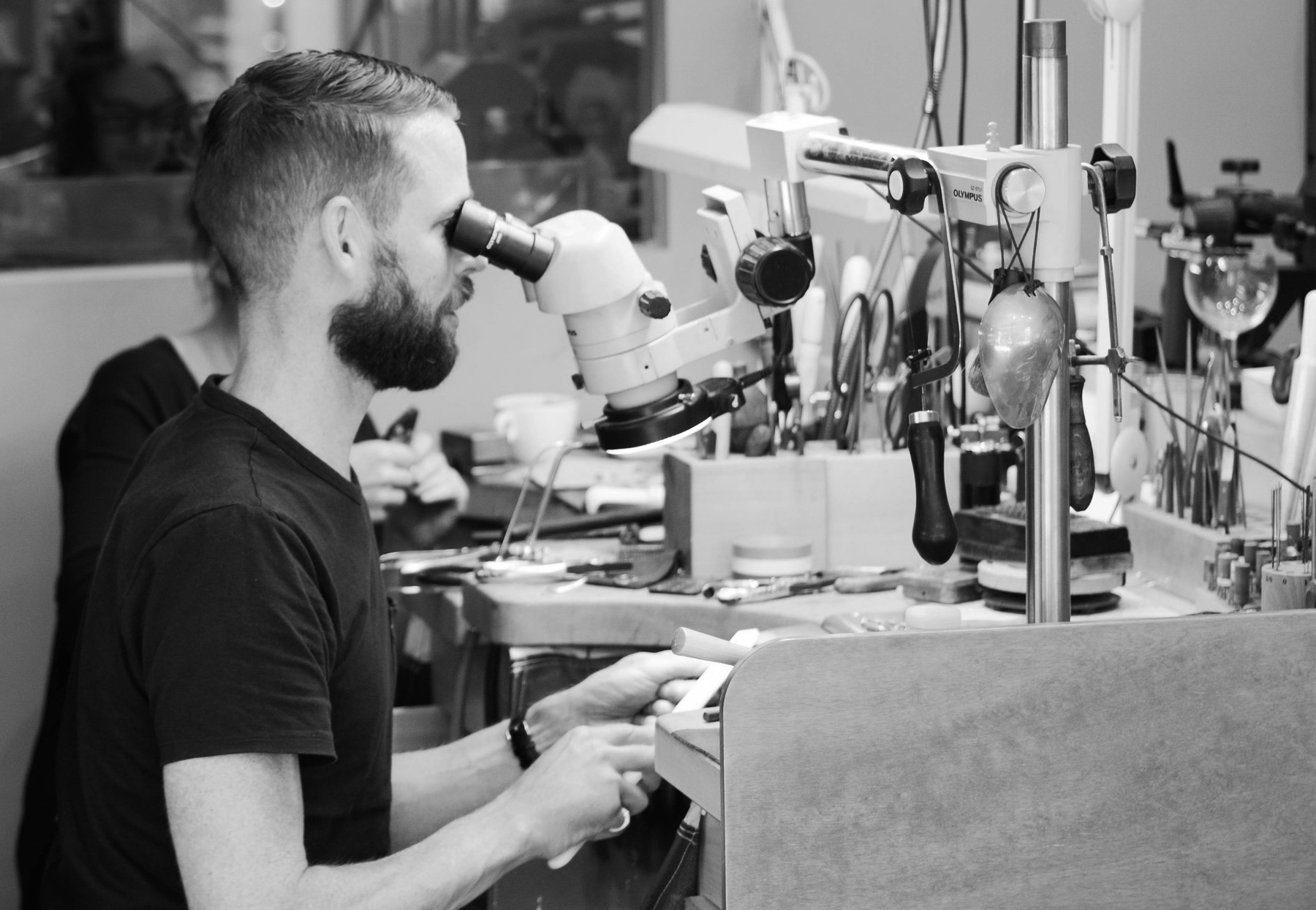
ACCURACY AND PRECISION
Each piece of our jewellery is made under a microscope for accuracy and precision. This level of detail is essential in order to create perfectly finished jewellery that will endure years of wear. We often set diamonds as small as 0.5mm in diameter and cut four tiny claws to secure each stone. Working under a cutting edge microscope ensures we can set each stone securely, even when working at this scale.
EXPERTS IN DIAMOND AND GEM SETTING
Diamonds and sumptuously coloured gemstones feature in many of our designs and each of these stones is set in-house. We have extensive experience in all styles of gem setting and are specialists in micro-pave diamond setting, having trained in Antwerp under one of Europe’s most highly regarded setters. There is a wide selection of diamonds and coloured stones in our collection to choose from, or if you have particular requirements we can source gemstones to suit. All of our diamonds and gemstones are sourced from trusted suppliers in the UK and Europe.
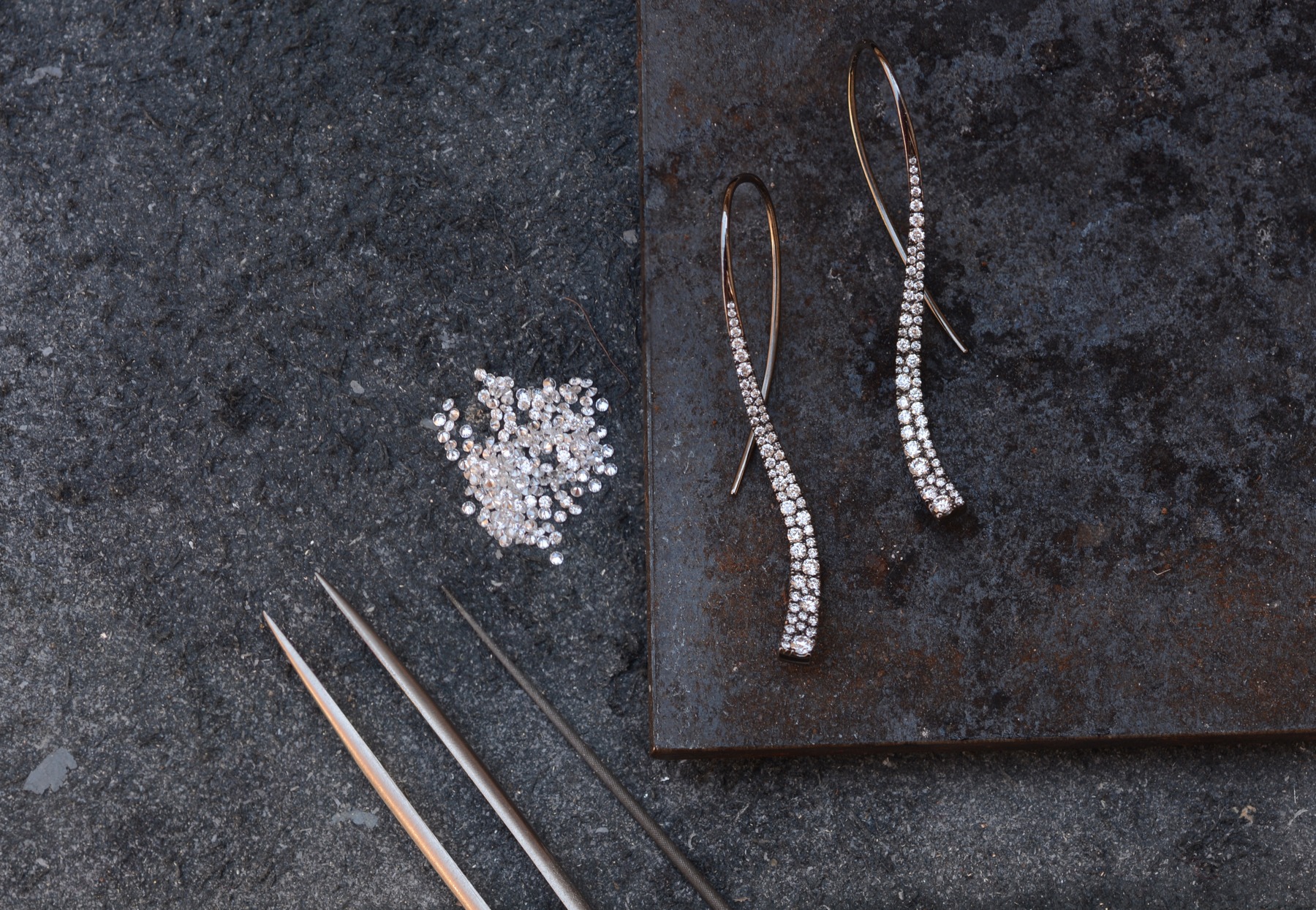
HAND-FORGING
Hand-forging is a centuries-old method of shaping metal with careful, methodical hammering that allows us to transform precious metal bar into fluid, tapering curves and loops. We use this traditional goldsmithing technique to create many of our signature designs, including our Twist engagement rings, forged earrings and the 18-carat gold and diamond cocktail ring seen here.
HAMMERING
Hammering can be used to create distinctive dimpled textures in metal. We use a customised hammer to create our signature hammered effect. The resulting texture has a raw, organic quality and a lovely dull lustre, as can be seen in the hammered men’s wedding rings to the right. Hammered rings can be created with flat or rounded profiles, and in your choice of metal and width.
HAND-CARVING
Many of our designs are carved by hand and are one-of-a-kind creations. Carving enables in wax allows us to create fluid, sculptural forms, such as those seen in our Arris series of one-of-a-kind rings. Carving has featured in our designs more and more recently. You can see examples in our collection and commission that range from delicate engagement rings to dramatic, sculptural cocktail rings. The carving process involves hand-sculpting wax to create a ring model that is sized to fit any gemstones perfectly. This wax model is then cast into precious metal, ready to be finished up, set and polished.